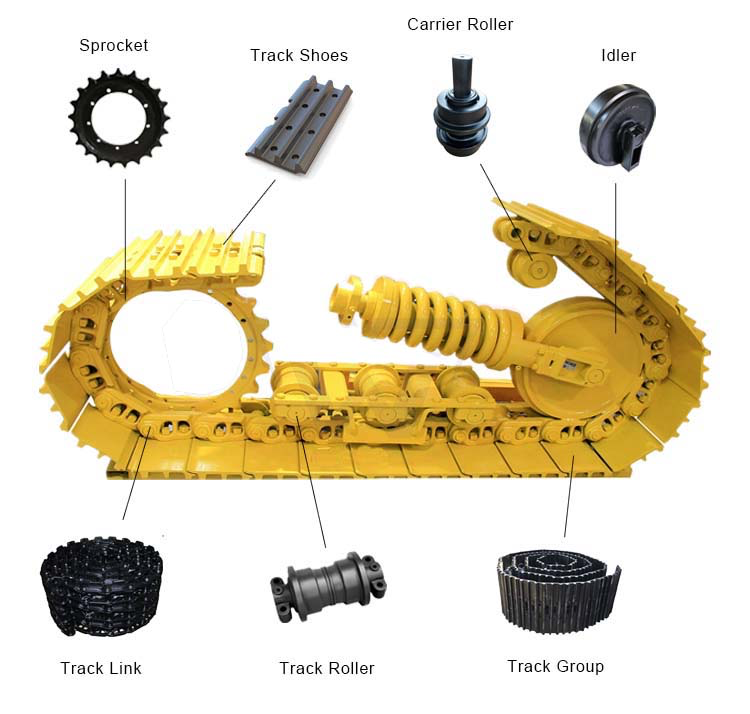
Track rollers
Track rollers, also known as lower rollers or bottom rollers, play an important role in increasing the stability and traction of excavators and bulldozers, especially when excavating and lifting heavy objects, they can provide greater stability and gripping force. Carrier rollers are typically made of materials such as steel, cast iron, steel plate, or composite materials to ensure that the machine has sufficient stability and durability during operation. Some high-end excavators and bulldozers may use composite materials to manufacture carrier rollers, which are typically composed of steel or aluminum alloys combined with other reinforcing materials such as carbon fiber. Composite material carrier rollers may have higher strength and lighter weight, but they are typically more expensive.
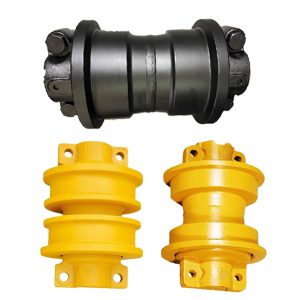
Carrier rollers
Carrier rollers, also known as top rollers or upper rollers, are used to support and drive the tracks of excavators and bulldozers. They rotate and drive the tracks through the gear transmission of the chain, allowing the machine to travel and operate. Carrier rollers not only provide transmission function but also serve to support the tracks. They support and guide the tracks during movement, ensuring smooth operation and maintaining the correct trajectory. Precision craftsmanship and appropriate materials are typically employed in the manufacturing process to ensure performance and durability. Balancing is conducted on carrier rollers to prevent vibration or imbalance during high-speed rotation.
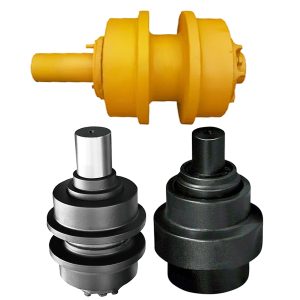
Driver sprockets
Sprockets provide additional traction through friction with the ground or working surface. They transmit power from the engine to the tracks by engaging with the track chain, propelling the machine forward or backward. Their materials possess high strength and hardness, suitable for manufacturing drive sprockets that need to withstand high loads and high-speed rotation. The selected material is then shaped into the original form of the drive sprocket through processes like casting, forging, or CNC machining. Subsequently, the processed drive sprocket may undergo heat treatment to enhance its hardness and wear resistance. Surface treatments such as galvanization, hot-dip galvanization, or coating may also be applied to increase corrosion resistance and surface hardness of the drive sprocket
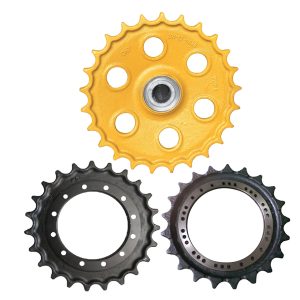
Front idlers
Front idlers are located at the top or side of the tracks, used to guide the tracks to maintain the correct trajectory, ensuring that excavators and bulldozers do not deviate from the track during movement. They reduce track wear by contacting the track, thereby extending the life of the tracks. They distribute the weight of the tracks and help reduce friction and wear on the tracks. Common materials used for high-quality front idlers of excavators and bulldozers include high-quality alloy steel, cast iron, or special alloy materials. These materials have high strength and hardness, suitable for manufacturing front idlers that need to withstand high loads. High-quality craftsmanship may involve surface treatments such as galvanization, hot-dip galvanization, or coating.
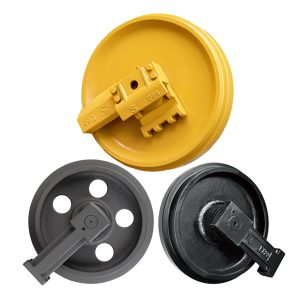
Track assembly
This includes track plates and chain assemblies. They are primarily used to drive the rotation of the track chain, providing propulsion for the machine. Track plates can adapt to various terrains, including soil, mud, and rocks, providing a stable operating environment for the machine. Compared to tires, tracks can distribute the weight of the machine and provide higher traction.
They are made of materials with high strength, wear resistance, and corrosion resistance, capable of withstanding the weight of the machine and complex working environments. The manufacturing process includes casting, forging, machining, and heat treatment processes to ensure that the track assembly has the required performance and durability.
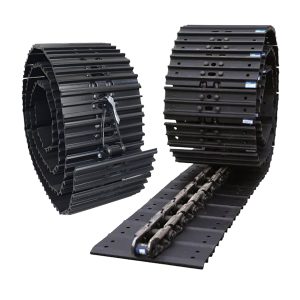
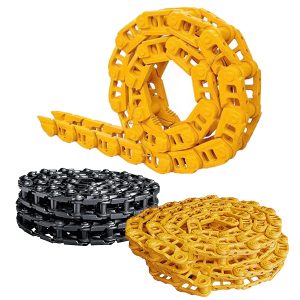